- Trail Insider
- Posts
- 3D Printing in MTB and tool design.
3D Printing in MTB and tool design.

3D printingInside info for MTB enthusiasts.
Welcome to the Trail Insider Newsletter! My name is Francoin. I’m an Industrial Designer in the cycling industry. My work is mostly the design of bicycles, tools and accessories.
TI is a newsletter for Mountain bike/Trail bike enthusiast who want to improve their riding, share ideas/tips about bike setup, maintenance and inside news in a global community of fellow riders.
Join the Trail Insider Crew!
📲 Scan the QR code to sign up for epic riding tips, gear insights, and trail stories delivered straight to your inbox! Already subscribed? Share this QR code with a friend who needs to ride with us! |
What’s inside this week:
1. The place of 3D printing in the cycling industry
2. Gadget of the week, a staple in the newsletter.
3. Shorts.
4. MTB video of the week.
The future of cycling: How 3D printing is revolutionizing bicycle frames, tools, and accessories
In the ever-evolving world of cycling, innovation is constantly reshaping the way bikes and their components are designed, manufactured, and used. One of the most exciting technological advancements in recent years is 3D printing—a process that is transforming bicycle frame development & construction, tool development, and accessory design. By enabling unprecedented customization, lightweight structures, and rapid prototyping, 3D printing is set to redefine the industry. But how exactly is this technology changing the cycling world? Let’s take a closer look.
Printed cheese… I can’t even.
The rise of 3D printing in bicycle frame design
Additive manufacturing
For decades, traditional materials such as steel, aluminum, carbon fiber, and titanium have dominated frame construction. Each of these materials has its own benefits and limitations, but they all share one thing in common: they rely on conventional manufacturing methods such as welding, molding, and machining. 3D printing (also known as additive manufacturing) is challenging these traditional methods by offering a completely new way to build frames.
Unparalleled customization
One of the biggest advantages of 3D printing in frame design is the ability to create fully customized geometries. Unlike traditional frame-building techniques that require expensive molds or labor-intensive welding processes, 3D printing allows manufacturers to create bespoke designs tailored to an individual rider’s body measurements, riding style, and preferences. Brands like Atherton Bikes and Moots are already leveraging this technology, using 3D-printed titanium lugs combined with carbon fiber tubing to create fully customizable, high-performance frames.
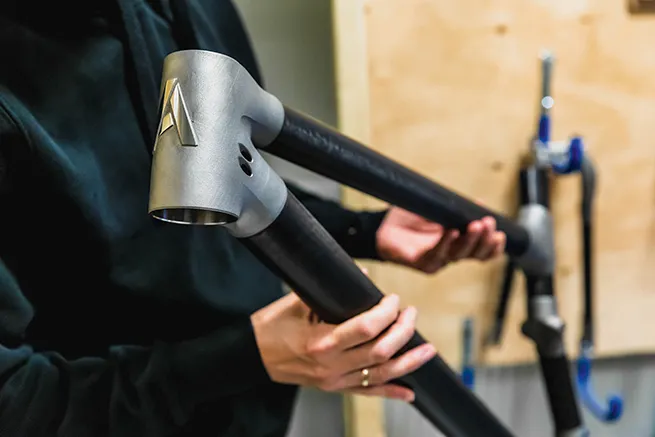
Atherton bikes are making 3D printed frame components popular in mountain bikes.
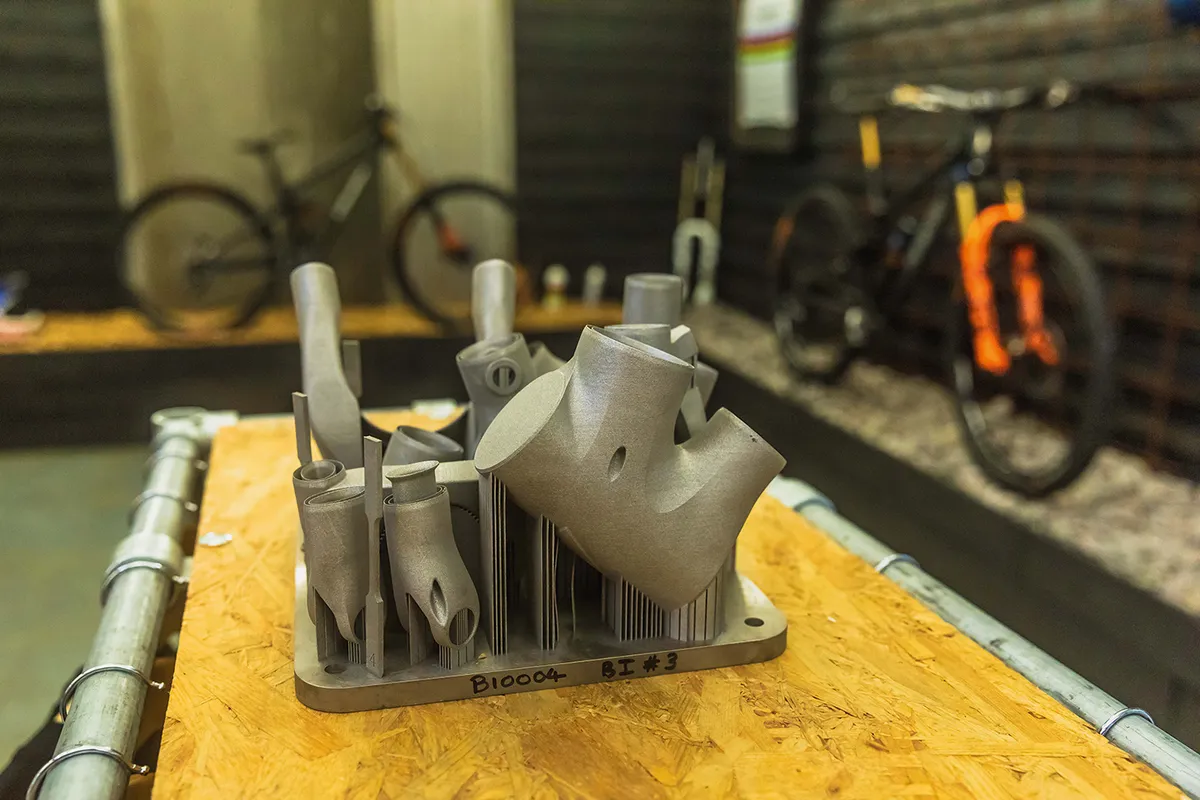
Various parts are printed on a single print bed, and then post processed to use as part of a frame.
Optimized strength-to-weight ratios
Another game-changing aspect of 3D printing is its ability to produce intricate lattice structures and organic designs that are both stronger and lighter than their conventionally manufactured counterparts. The layering process of additive manufacturing enables engineers to optimize material distribution, reinforcing high-stress areas while reducing unnecessary weight elsewhere. This approach is particularly beneficial for mountain biking and endurance road cycling, where weight and durability are crucial factors.
Sustainability & waste reduction
Traditional manufacturing methods often result in significant material waste—whether it’s carbon fiber offcuts or metal shavings from CNC machining. 3D printing, however, is inherently more sustainable because it builds components layer by layer, using only the material necessary for the final product. Additionally, some manufacturers are experimenting with recycled materials in 3D printing processes, further reducing the environmental impact of bicycle production.
3D printing in cycling tools & accessories
While frame design is arguably the most high-profile application of 3D printing in cycling, this technology is also making waves in tools and accessories, offering innovative solutions that were previously impossible or impractical to manufacture.
Precision and efficiency in tool design
Cyclists and mechanics often rely on Ryder Innovation tools for bike maintenance and repairs, and 3D printing allows us to create highly specific, task-oriented tools that are considered and optimized. Ryder Innovation uses 3D printing to develop compact, multi-functional repair tools that minimize bulk while maximizing usability and ergonomics

Complex tools can be 3D printed before molds are opened to make sure that everything works as intended.
Printing streamlines the prototyping process and fast-tracks development.
With 3D printing, tools can also be made on demand, eliminating the need for mass production and large inventories. This is especially useful for professional mechanics who need customized solutions for high-end bikes with proprietary components.
Revolutionizing accessories: From saddles to bottle cages
Accessories may seem like small details, but in cycling, every gram and every ergonomic advantage counts. 3D-printed saddles, such as those developed by Specialized and Fizik, have already gained popularity for their adaptive padding and tunable ride comfort. These saddles feature complex lattice structures that provide better pressure distribution and shock absorption compared to traditional foam-based saddles.
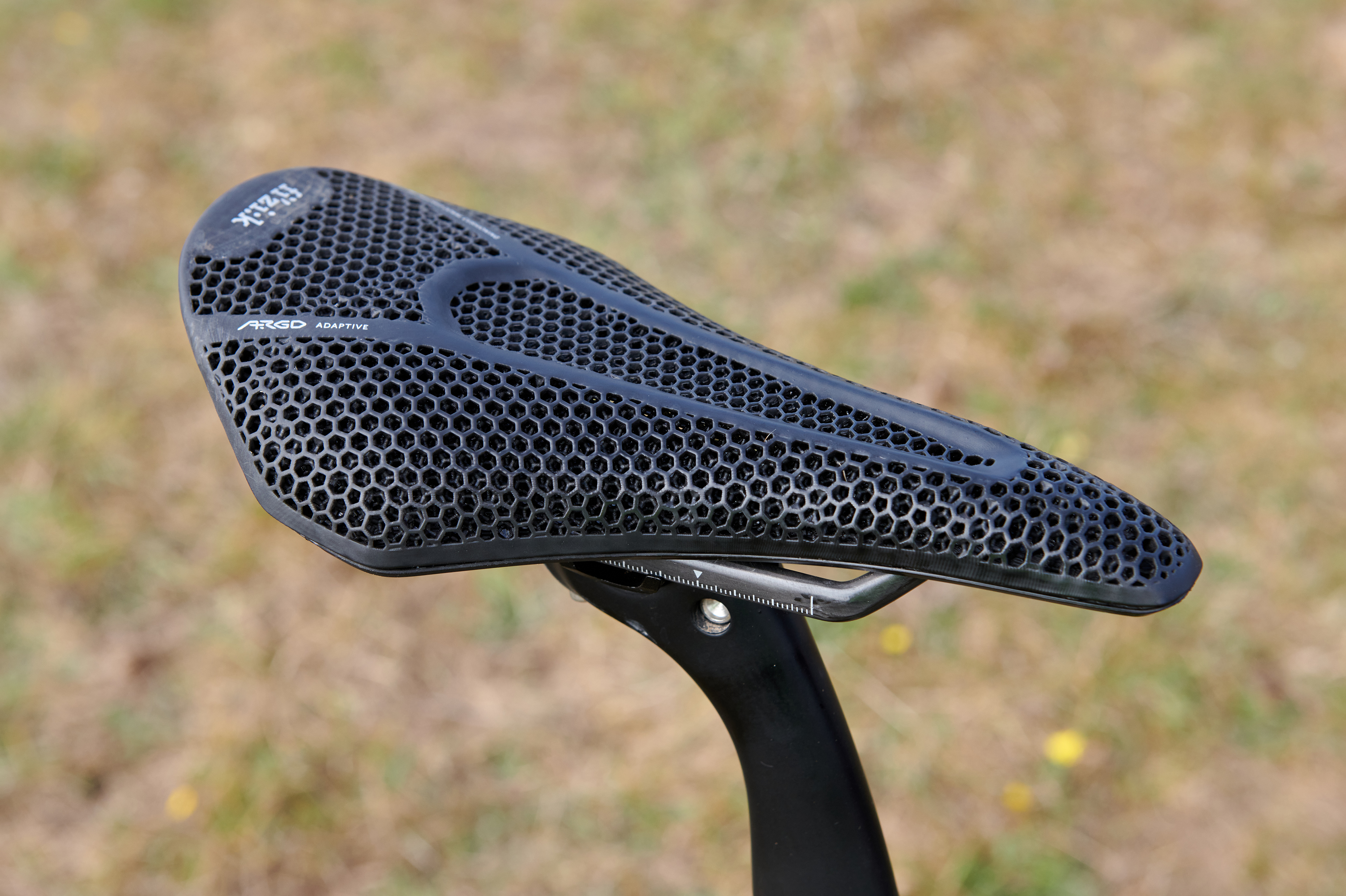
With varying mesh density and tuned lattice structure, you can build in zone specific padding (more or less as needed) in a lightweight saddle. Smart stuff!
Prototyping & rapid development: The true power of 3D printing
Perhaps the most underrated advantage of 3D printing in the cycling industry is its role in prototyping and product development. In the past, developing a new bike frame or accessory required labor intensive work for prototypes, expensive molds, long lead times, and multiple iterations before reaching production. With 3D printing, designers can create, test, and refine prototypes in a matter of days or weeks, rather than months creating highly accurate, to-scale prototypes. I often print full size frames in sections on my small 3D printer, and can then use this to get a better feeling for the shapes and clearances than on a 3D model on the computer.

Printing is not all moonshine and roses. This is a complete rear end split into pieces… 31hours into a 40 hour print I walked into my office to see this mess.
A finished print is close to the real thing and dimensional accurate, and can be fitted with parts.
For instance, companies like Hope Technology and Zini Bicycles use 3D printing to develop new frame geometries, test aerodynamic features, and tweak suspension designs before committing to full-scale production. This rapid iteration process allows for faster innovation, giving riders access to cutting-edge technology sooner than ever before.
Challenges & future potential
Despite its many advantages, 3D printing in cycling is not without its challenges. Cost remains a significant barrier, particularly when it comes to high-performance materials like titanium and carbon fiber composites. Additionally, scalability is still an issue—while 3D printing excels in custom, low-volume production, it has yet to match the cost efficiency of mass production techniques for mainstream bikes and accessories.
However, as 3D printing technology continues to advance, we can expect further breakthroughs in material science, printing speed, and production scalability. More brands are likely to adopt hybrid manufacturing approaches, combining 3D-printed components with traditional materials to push the boundaries of what’s possible in cycling design.
For me, the single most important benefit is the streamlined process of design to manufacture.
A new era of bicycle innovation
3D printing is no longer just a futuristic concept—it’s actively shaping the future of cycling. From custom-fitted, lightweight frames to ergonomic accessories and precision-engineered tools, this technology is unlocking new possibilities for performance, sustainability, and design flexibility.
As costs come down and techniques improve, we can expect 3D printing to become a mainstream part of bike manufacturing, offering riders more personalization, durability, and innovation than ever before. Whether you’re a competitive racer, a weekend warrior, a cycling industry insider or just enjoy using quality tools, one thing is clear: the future of cycling is being printed, one layer at a time.
Gadget of the week: 3D printer. Creality CR6SE
I have a pretty basic Creality CR6SE printer that I’ve put through the ringer and it is still going. It has a small bed size of 235 × 235 × 250mm and for bigger parts I split them into separate sections.
This is used almost as much as my PC, and regularly runs overnight printing a frame, tool or accessory.
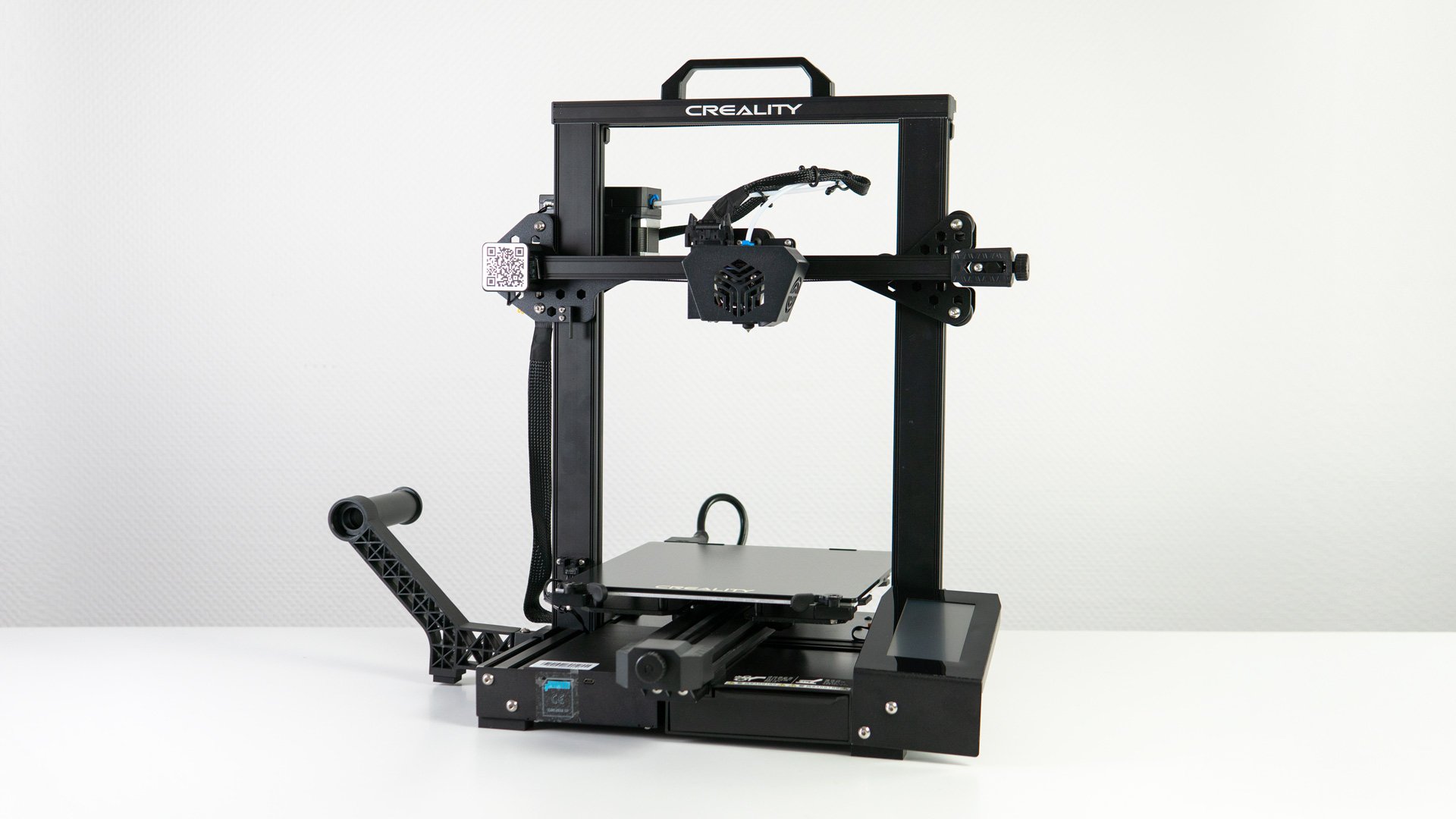
Horses for courses - you really don’t need a big expensive printer to get printing.
Shorts:
Q. Is a 3D printer a good idea if I’m not a designer?
A. Absolutely! While having design skills helps, many ready-made 3D models are available online for bike tools, mounts, and accessories. Modern slicer software (I use Cura) makes printing user-friendly, and you can experiment with modifications over time. If you love tinkering and problem-solving, a 3D printer can be a game-changer for customizing and prototyping bike parts—even without advanced CAD skills! 🚴♂️🔧
Q. What is a slicer
A. A slicer is software that converts a 3D model into instructions (G-code) for your 3D printer. It "slices" the model into thin horizontal layers and determines how the printer will build each one, including settings like print speed, layer height, infill density, and support structures. Popular slicers like Cura, PrusaSlicer, and Simplify3D let you fine-tune your prints for the best balance of speed, strength, and quality. Think of it as the middleman between your design and the final printed object! 🖨️🚴♂️
Video of the week:
Joe Connell ‘surfing’ his bike on some prime Scottish dirt.
About the author:
Hello, I’m Francoin, an Industrial Designer in the cycling industry based in Somerset West, South Africa.
Tools, lights, accessories and bicycle design is my daily graft.
This newsletter is to share some of the experience & industry insight that I pick up along the way, with fellow cyclists. If you are new to the sport, or been riding for many years, I plan to give you something of interest in every edition.
Thanks for subscribing and Happy trails!
FV

Connect on Linkedin, or follow us on Instagram and share with your riding buddies.
Also let us know if you have any specific topics that you would like covered here for your coffee time reading.